Quite simply, we help steelmakers make steel better
Let's work together
Whether you manage a small steel mill or a fortune 500 steel corporation
Steel Hub can help you enhance your operational and financial performance to create a more efficient, future-ready enterprise.
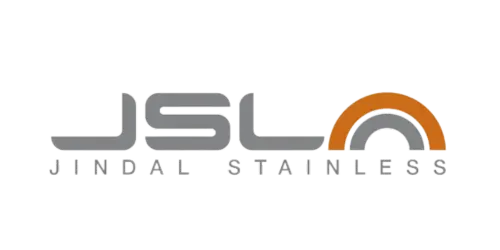
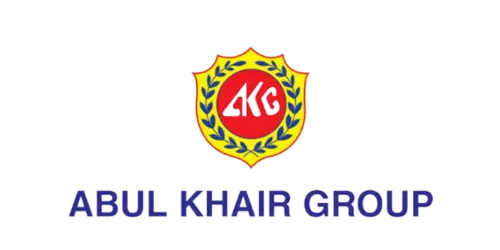
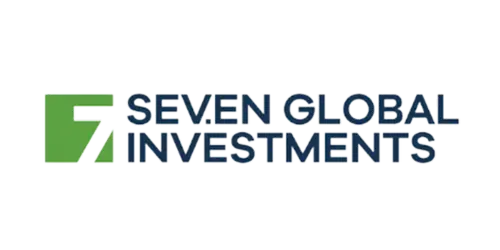
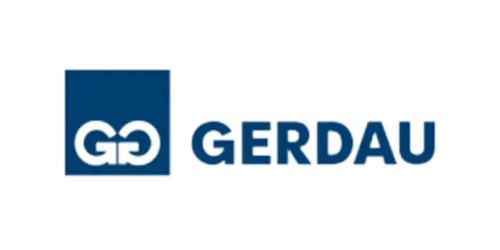
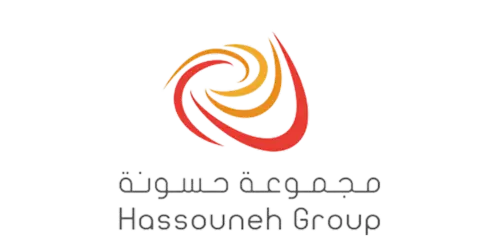
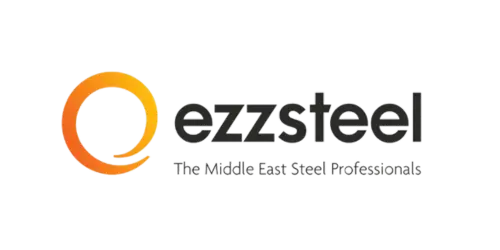
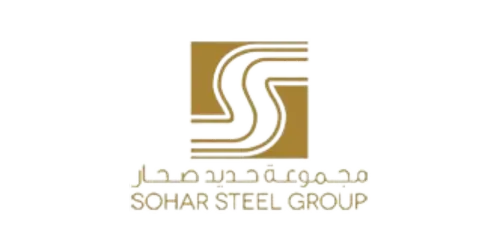
Expert Solutions for the Steel Industry
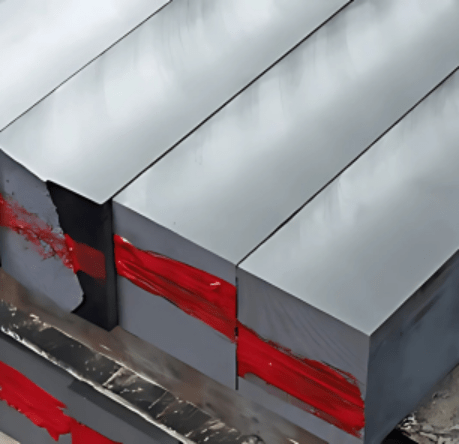
Services include:
- Process Intelligence & Digitalisation
- Product Range Expansion
- CAPEX Strategy
Steel Advisory
Steel plants operate in fast-moving, complex environments where even small inefficiencies can lead to major losses. Steel Hub combines proprietary software and in-depth industry expertise to help steelmakers gain a transparent view of their operations. We analyse material and information flow, quality, logistics, and IT/automation readiness to identify high-impact improvement opportunities. Our team supports steel plant managers, owners, and C-suite executives in expanding product ranges, improving margins, and planning capital investments that deliver real returns.
Your advantage:
- Transparent overview of operations and processes
- Targeted, high-ROI improvement programs
- Data-driven capital investment prioritization
- Reduced costs through better resource allocation
- Clear roadmap for digital, lean, and green transformation
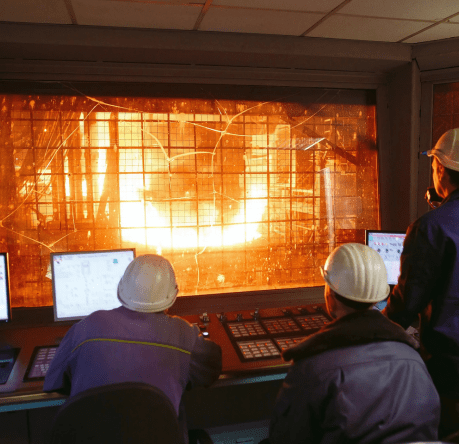
Services include:
- Performance Diagnostics
- Production Process Optimisation
- Change Management for operational transformation
- Defect troubleshooting and solutions
Performance Improvement
Steel Hub boosts productivity and reduces waste through targeted performance diagnostics and process optimisation. We use a combination of AI-powered analytics, lean methods, and practical shop-floor experience to increase throughput, improve yield, and address persistent quality issues. From technical fixes to organisational change management, we help teams implement lasting improvements.
Improvement initiatives often fail because they target symptoms instead of root causes. Our diagnostics surface hidden inefficiencies and operational gaps that drag down performance. In many steel plants, energy waste, defects, and unoptimised processes create “invisible losses” that significantly affect the bottom line.
Your advantage:
- Increased throughput and yield with minimal downtime
- Reduced cost per ton by lowering scrap, rework, and energy use
- Practical solutions for persistent quality defects
- Short payback periods for low-CAPEX energy and process improvements
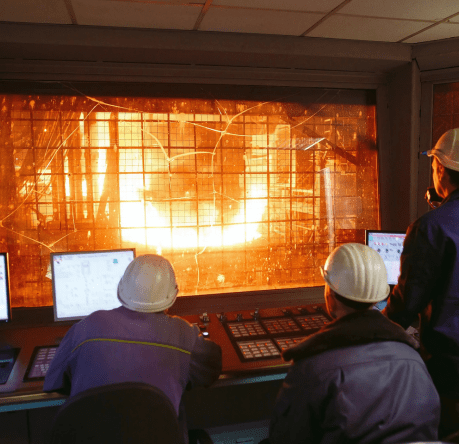
Services include:
- Performance Diagnostics
- Production Process Optimisation
- Defect Troubleshooting and Solutions
- Change Management for Operational Transformation
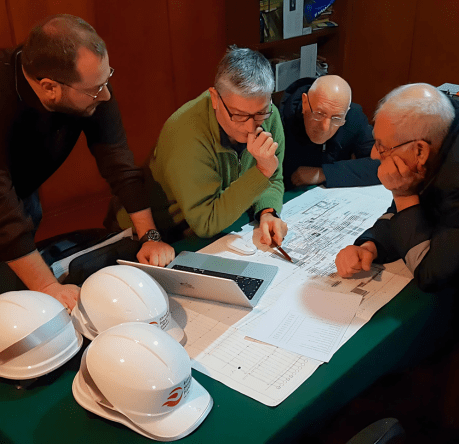
Services include:
- Operational Due Diligence
- Commercial Due Diligence
Due Diligence
Steel Hub conducts rigorous operational and commercial due diligence for M&A, CAPEX validation, and strategic planning. We assess steel production assets, processes, risks, and market positioning to provide an accurate picture of performance and potential. Our expert teams include both technical specialists and market analysts, offering a 360° view tailored to the unique demands of the steel industry.
Steel assets are capital-intensive and technically complex—yet key performance risks often remain hidden in traditional financial reporting. Buyers and investors need a reliable view of how assets perform relative to their true potential.
Our focused approach ensures both technical and market risks are identified before investment decisions are made.
Your advantage:
- Validation of technical claims and performance metrics
- Early identification of bottlenecks, inefficiencies, and hidden costs
- Scenario models for growth projections and CAPEX planning
- Strategic recommendations from industry experts
What our clients say
Take the first step with Steel Hub
Request a consultation with one of our skilled consultants, and let’s embark on a journey to unlock your full potential.