Abstract
- Wind, solar and nuclear capacity will need to grow by the factor of 6 to enable green hydrogen production at a level that is sufficient for a decarbonization of CO2-intense industrial processes
- Investments required to make European steel production carbon-neutral may reach up to EUR 100 bn1 (for Europe alone)
- Steel produced by green hydrogen may reach cost-competitiveness after 2030, depending on various factors including CO2 price regulation
Formidable challenges to co2-neutral steel production at a large scale
On February 2021, a newly announced EUR 2.5 bn green hydrogen steel venture named H2 Green Steel claimed2 it will start production as early as 2024. It joins a long list of proposed EU green steel projects3 incorporating technologies such as hydrogen, hybrid blast furnaces, and carbon capture and storage.
And while there is growing industry consensus that hydrogen-based technology might be the key to begin the process of decarbonizing the European steel industry to meet the the EU’s 2050 CO2 reduction goal, the underlying challenges are formidable:
- Lack of renewable energy: The International Renewable Energy Agency (IRENA) says the world will need between 133.8 and 158.3 million tons of green hydrogen a year to decarbonise processes such as long-term energy storage, shipping, heating as well as cement and steelmaking. Rechargenews.com calculates that wind, solar and nuclear energy capacity would need to grow from its current (2018) 1,441 GW capacity to 9,215 GW (or by the factor 6.4) by 2050 and be solely devoted to producing green hydrogen to deliver those 133.8 million tons of green hydrogen4.
- EUR 100 bn+ in new investments are needed to make European iron-ore based steel climate neutral. If steelmakers are expected to bear this cost alone, their steel will simply not be price-competitive in the world markets.
- H2 DRI (hydrogen direct reduction iron) has yet to be proven on a large scale.
Encouraging developments that may help to tackle these challenges
These three challenges in transitioning towards fossil-free steel are enormous. However, some early signs of progress towards the required transition are observable:
- Regions that already have sizable renewable energy assets and potential for extended expansion may lead the way. Sweden and Finland, for example, “overproduce” renewable energy on windy, sunny days. Therefore, storing “extra” energy as green hydrogen makes sense already now and might contribute to power new EAFs on cold, dark or windless days. A leading Swedish H2 DRI enterprise, HYBRIT Development, includes energy company Vattenfall as one of its partners. Vattenfall plans on adding 15 TWh of annual renewable energy capacity to specifically supply HYBRIT’s all fossil-free iron and
v steel production by the target date of 20455. - Basic H2 DRI technology has been around in laboratories for decades. Arguably, the hydrogen reduction pilot plant that is furthest along is HYBRIT’s near Luleå, Sweden. During operation, it processes one ton of iron ore per hour and has been operational since fall 2020. HYBRIT’s stated goal is to offer iron ore-based, fossil-free steel for commercial use in 2026 — and, naturally, they are actively seeking licensees for their hydrogen reduction technologies6.
- The list of proposed green steel projects7 mentioned above is facilitated by sizeable investments by governments and the EU. However, steel companies will need to receive significantly higher subsidies/tax incentives to drive the transition to greener production.
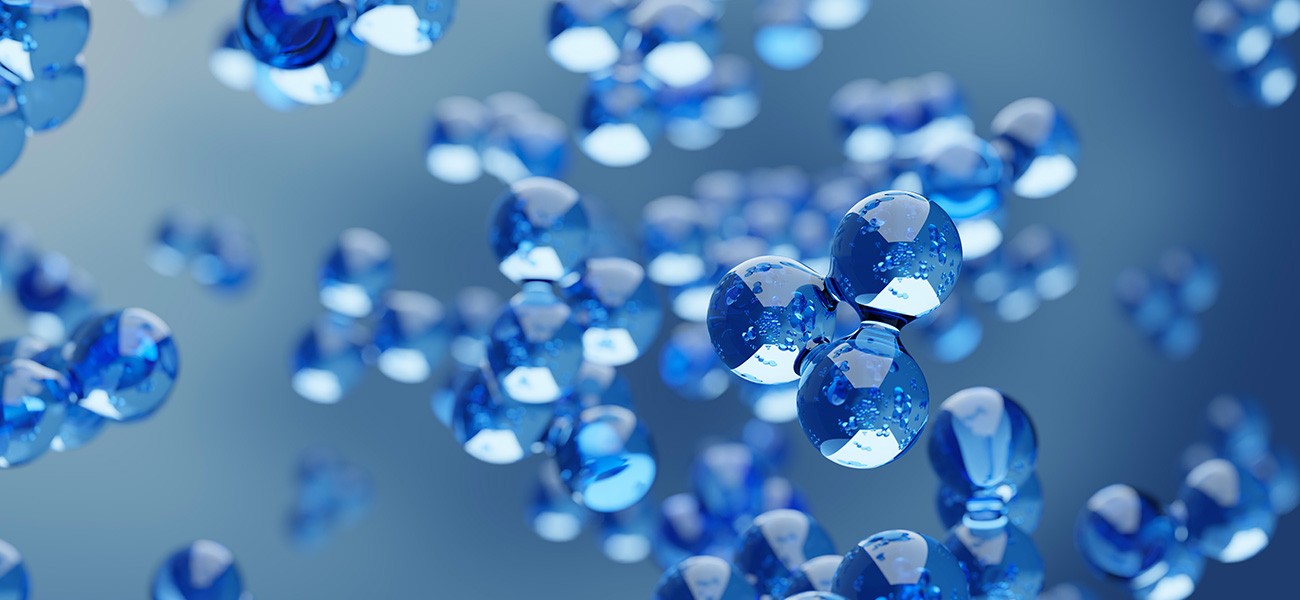
Economic factors to be considered to drive the transition
Initially, H2 DRI steel is estimated to cost 10% to 30% more, likely limiting the first offerings to high-quality, high-value steels such as advanced high-strength steel (AHSS) for automotive safety and light-weight applications. The price mark-ups for carbon-neutral steel will be driven by multiple factors including carbon cost (emissions trading/taxes), renewable energy cost rates (mainly for the production of ‘green’ hydrogen, but also to power EAFs, etc.), the economies of scale of large electrolyzers, the amount of government subsidies/tax incentives offered for the transition, and how governments protect decarbonized steel producers from high-emissions steel imports.
A global approach on this effort is mandatory: if only the EU and US governments push for hydrogen-based steel production at a higher cost, production will simply move to developing countries with lower environmental restrictions. The results would be catastrophic for EU and US steel companies while doing nothing to help the environment.
In April 2020, McKinsey & Company created a cost competitiveness study of pure hydrogen-based steel production based on green hydrogen’s cost decline and carbon dioxide’s price rise. It concluded that with CO2 at EUR 55/ton and hydrogen at EUR 1780/ton (implying an electricity price of EUR 0.027/kWh), conventional steel would retain a cash cost advantage. McKinsey predicted that pure hydrogen-based steel production may become cost-competitive between 2030 and 20408.
Indeed, the price of a European allowance to emit a ton of CO2 has doubled since March 2020 and has reached a new all-time high of EUR ~40 in March 2021. In February 2021, investment firm Northlander anticipated carbon prices of between EUR 50 per ton this year and 70 EUR in 2025, while Andurand Capital Management thinks EUR 100/ton is possible later this year (2021)9. A sustained spike in carbon prices would likely lead to a virtuous spiral: Green hydrogen becomes comparatively less expensive, more and larger electrolyzers are built — providing greater economies of scale and making green hydrogen production less expensive, leading to wider hydrogen use, and so on.
If experimental hydrogen steelmaking technology can prove its effectiveness (i.e., being cost-competitive and environmentally friendly), hydrogen — grey, blue, but eventually mostly green — will be used in the coming years to incrementally transition many brownfield steel plants into becoming more carbon-efficient producers. Then, from 2030 to 2050, large-scale, completely carbon-neutral H2 DRI steel plants will come online, offering increasingly competitive steel prices.
The pure hydrogen-based steel production transition planning should be completed within the next 5 (or at most, 10) years to meet the 2050 CO2 goals. This is due to its high complexity and associated CAPEX requirements — not only at the steel mills and iron ore mines, but also for the extensive infrastructures for renewable energy, electrolyzers, hydrogen storage and distribution. In other words, the entire steel production value chain must be decarbonized as well.
As a technical consulting firm to the industry’s leading steel producers, Steel Hub has in-depth knowledge of the technical, financial and environmental capabilities as well as constraints present nowadays. Considering the full range of options to improve efficiency, reduce energy consumption and emissions along the entire steel production process chain, it is important to understand which technologies are ideal depending on respective plant setup and location.
The transition to greener steel production has started, and planning needs to take place now. We are available to discuss your individual needs in this context.
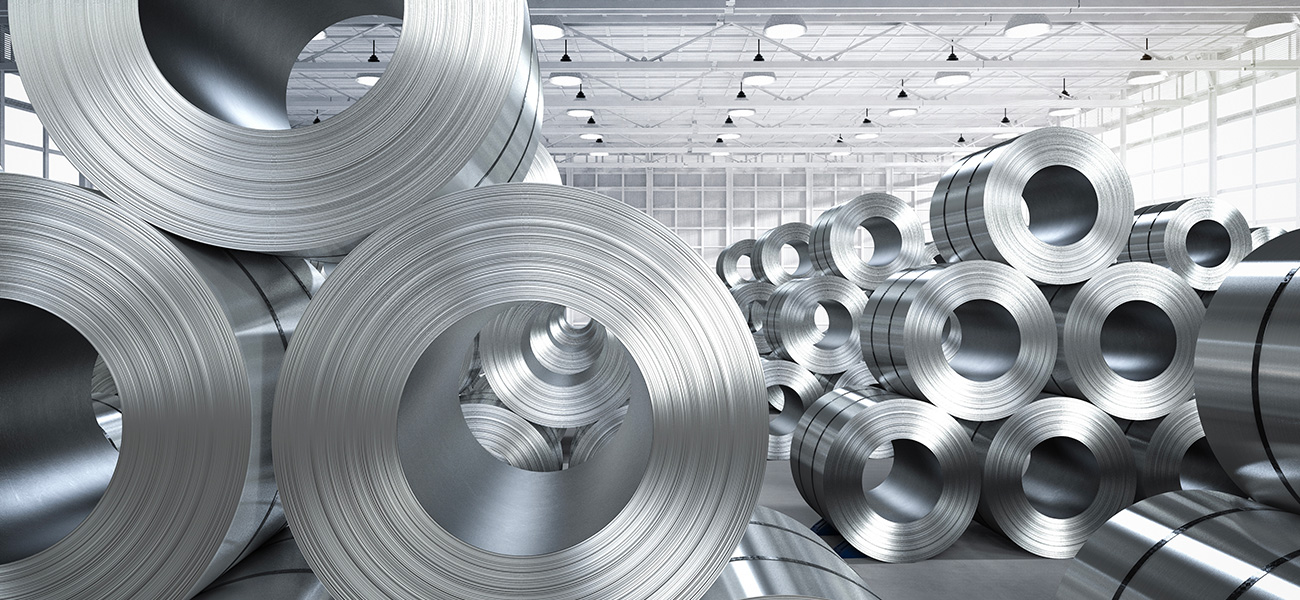