Key Takeaways
Here are five key takeaways from this document:
Problem: An Eastern European steel plant was underperforming, with low yield, high energy use, and inefficient scrap management. Budget for capital investments was very limited.
Challenge: Key issues included long tap-to-tap times, outdated practices, and energy consumption far above benchmarks. Scrap operations and burner performance were also below standard.
Solution: Steel Hub launched a low-capex operational excellence programme focused on technical fixes and operator mindset. Daily briefings, shop-floor presence, and revised incentives drove engagement.
Improvement: Technical fixes included automated temperature control, magnet platforms, improved scrap charging, and reduced manual reporting. These targeted both process efficiency and energy savings.
Impact: EAF power-off time was reduced by one-third, yield improved by 15%, and electricity use dropped by 5%. All results were delivered with less than 1 million USD in investment.
Overview
Situation
The steel plant is located in Eastern Europe and manufacture steel reinforcing bars, with an output of 350.000 tons p.a. Due to a dissatisfactory operational performance of the plant, the plant management requested a technical and economic plant assessment to identify improvement potentials. There was only very limited budget for capital expenditure.
Initial review brought the following results:
Yield was well-below optimal level and potential, and plant productivity well-below European benchmark levels
Tap-to-tap time was far longer than in any other plant in the client’s portfolio
Plant energy consumption was unusually high
Scrap management did not meet best-practice standards and caused significant disruptions to
EAF operations EAF burners were not optimised
The end-of-heat liquid steel practice was not applied
Following this initial review, the plant management requested an operational excellence program, which we delivered.
Approach
Approach
The operational excellence program started by ensuring that we had both full backing from plant management and plant ownership. In our experience, very often the human factor is the single one variable having the largest impact. Besides working on the mindset and capabilities of operators, we took only low-capex improvement measures into consideration.
We introduced the following improvements:
“Soft measures” targeting operator mindsets and capabilities”
Following this initial review, the plant management requested an operational excellence program, which we delivered.
We aligned with plant management on the priorities of the EAF performance improvement program
We introduced a daily routine: We started every morning with a ~15 minute meeting involving plant management and leading engineers to review special incidents and behaviour of the previous day
We showed presence on the shop floor, moving the management office inside the furnace cabin
We discussed improvement ideas with operators on a 1:1 basis
We held a performance review together with plant operators every ~2 months to inform and keep them motivated about the technical and financial impacts of their improvement efforts
We adjusted the salary / bonus structure to set appropriate yield and energy consumption targets for the monetary incentivization of the plant crew (previously, targets had been too low / easy to achieve)
Low-capex technical fixes
We switched from manual/human temperature to automatic/robot temperature control to reduce furnace power-off times
We installed an automatic delay reporting system to replace time-consuming manual reporting processes
We increased charges per scrap bucket through a mix of creative adjustment measures
We installed four magnet platforms by the scrap yard to improve the quality of scrap disposed and reused—the scrap metal content jumped from 9 to 18%
We introduced end-of-heat liquid steel practice to reduce electricity required for melting the next load of scrap
We tweaked the chemical burner mix to reduce electricity consumption
Results
After the initial phase during which were introduced these improvement measures, we still gave support to the plant management, reviewing progress on improvement initiatives regularly.
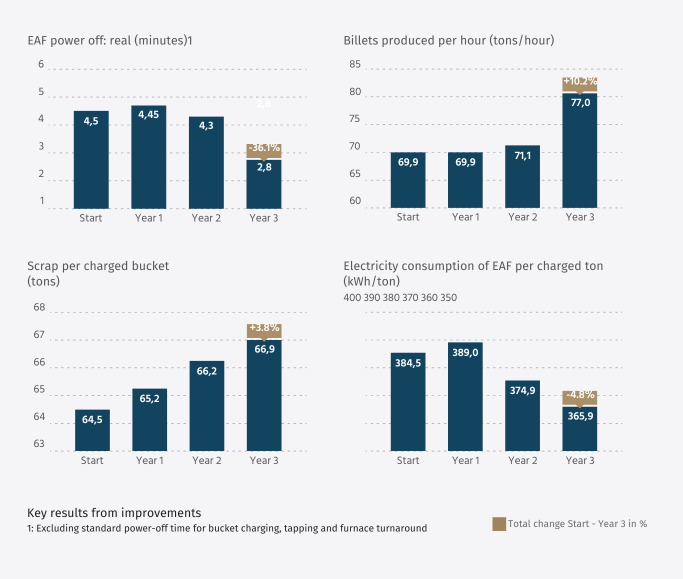
Three years after the beginning of joint efforts, the real EAF power-off time could be reduced by a third, and yield increased by 15%. We managed to increase scrap per charged bucket by 4%, and the measures of the operational excellence program reduced EAF electricity consumption by 5%.
We would like to restate the fact that large impact does not necessarily need to cost a significant amount of money. Most of the behavioural changes did not require any significant expense, and the technical fixes could be delivered with minor capital expenditure. All results shown in this section could be delivered with a total capex investment smaller than 1 million USD.
After the conclusion of this improvement program driven by very low-capex measures, as a next step, the plant management is now assessing the possibility of improving the performance further through the installation of a chemical package for the EAF.